Everything You Need to Know About Nitinol
Nitinol (pronounced night-in-all) is a metal alloy with unique properties and uses. This amazing metal alloy can “remember” or change shape depending on temperature. Before you decide whether to use nitinol in your medical device design, here are some things you should know about it.
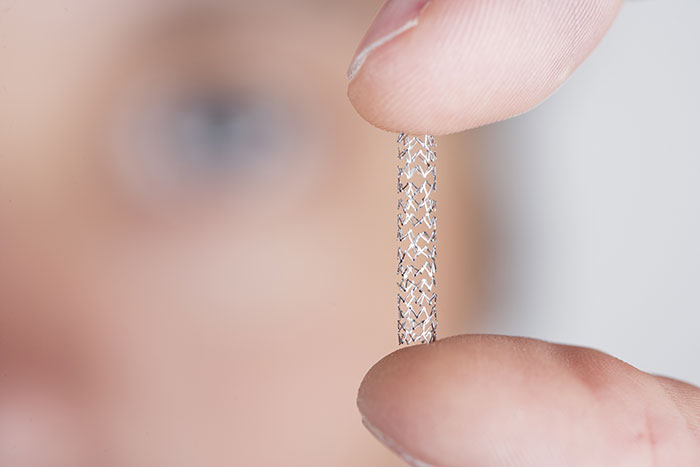
How was nitinol developed?
Nitinol originated in 1959 by mistake. Scientists were developing a heat and corrosive resistant alloy and during that process, created an alloy made of 55% nickel and 45% titanium. The name represents its elemental components and place of origin. The “Ni” and “Ti” are the atomic symbols for nickel and titanium and the “NOL” stands for Naval Ordinance Laboratory, the lab that discovered it.
Where is nitinol used?
Nitinol has been around since the early 1960s but was unavailable commercially until twenty years later due to the tight controls needed in the manufacturing process. Since then, it has become an important material for robotics and medical devices. Nitinol is superelastic (10X as flexible as other metals), and its thermal shape memory properties are unlike any other material available.
Applications with tight space requirements often use nitinol when conventional mechanisms cannot fit. One such application is where a device or structure needs to be inserted thru a small opening and then released to open to a larger set size. A compressed nitinol wire or structure is inserted into a small delivery tube and then placed in position. Once deployed, the nitinol structure opens in size to several times the diameter of the delivery tube.
How does nitinol work?
One of the most valuable properties of nitinol is the two-way shape memory effect. This shape memory effect is when the metal undergoes a reversible phase transformation between the Austenite and Martensite phases. The atoms of metals are arranged in specific structures, depending on their components, but rarely change structure shape while still solid.
Under high temperatures, the metal enters the Austenite phase. In this phase, it achieves maximum stiffness and is spring-like when bent. The metal enters the Martensite phase during low temperatures. In this phase, the metal feels rubbery and bends easily. When nitinol is in its Martensitic form, it can easily deform into a new shape. However, when heated through its transformation temperature, it reverts to Austenite and recovers its previous shape.
Slight changes in the alloy composition or heat treatment adjust the temperature at which nitinol remembers its high-temperature form. The device’s use determines which transition temperature you choose. For example, if you were making a medical device, such as a stent, you would select a transition temperature close to or equal to human body temperature.
What are some real-world nitinol applications?
Robotics engineers often use nitinol as an actuator. In this case, they apply an electrical current (or heat) to a stretched nitinol wire. The wire contracts while the charge is applied and relaxes once it stops. Unlike most metals, Nitinol contracts in length when heated but will maintain the same absolute volume. Also, its thermal movement is 100 times greater than other metals.
A bone staple is one example of nitinol thermal size contraction. The staple is stretched open and inserted into two holes in the bone and then heated to return to the original shape. This technique effectively pulls the two pieces together and holds them in place during the healing process.
Another example is a stent which is cooled and mechanically squeezed to fit into a small diameter catheter inserted through a vein. Once positioned, the stent is released from the constraining sleeve and, after reaching body temperature, returns to its original shape, holding the artery open.
For elastic deployment, Nitinol wire is mechanically held in place using a fixture and then heated in a fluidized temperature bath, at a prescribed temperature and time, before being quickly submerged in cool water. Once removed from the fixture the wire retains its shape regardless of the angle or intensity of deformation. When let go, the wire returns to its set shape. There are numerous real-world examples of this application, such as The Homer Mammalok needle/wire localizer. The device feeds a curved wire through a straight cannula, and upon exiting, it curves into its original “J” shape. The user can repeat this process dozens of times without the wire deforming.
What are the common challenges when using nitinol?
One challenge when working with nitinol is determining the best method for attaching one wire to another. Depending on their phase, the wires can be very elastic or stiff, making them difficult to weld or bond. One method involves mechanically crimping wires together using other materials like stainless steel. These crimps can then be TIG welded to other components to form the desired end product.